Polymeric processing
Thermoplastic processing is dominated by the Archimedes screw, which is a long screw, fitted in a pipe and used to pump liquids, slurries, sewage and other difficult media. For thermoplastic purposes the screw is tightly fitted in a temperature controlled extruder barrel fed by plastic granules from a hopper and the plastic is heated by the kneading action of the screw combined with external heating of the extruder barrel.
In order to create pressure in the extruder the pitch height of the screw is reduced along the screw from the feeding zone to the melt zone and to the metering zone. For an extruder, the cylinder barrel ends in a filter package and a die to shape the extrudate. This creates a back pressure that helps to melt and homogenize the plastic material. Injection moulding is also based on the Archimedes screw with the added feature to stop the screw and move it axially forward to push molten plastic into a mould in order for it to cool down and take on the shape dictated by the mould cavity.
The shape of the extruder die determines the shape of the extrudate that may be further manipulated by, for instance, an inner air pressure of a tubular extrudate to make plastic film or by pulling of the multifilament that comes out during melt spinning in order to orient the polymers for improved strength and stiffness. Blow moulding is an intermittent technique used to make hollow objects such as bottles that share some elements of the extrusion process. During the intermittent processes where the screw is moved axially in order to push molten plastic out, there are possibilities and limitations to the process cycle. In particular the injection moulding cycle is rather special. Once the mould is filled, the material shrinks during cooling. In order to handle that shrinkage and make sure the mould is properly filled every time, additional material is squeezed in by overfilling it by adding an after pressure that compresses the molten plastic. A molten plastic is, unlike most low molecular fluids, actually compressible.
Once the mould inlets have solidified it seals the mould and filling of new granules into the screw channel can start while the moulded object continues to cool and be ready for ejection. The limiting factor here is the cooling phase from injection to ejection and it depends highly on the chosen material. This is affected by the temperature the material has to cool from until it is solid enough for ejection and also whether it crystallizes, a process that requires management of both the exothermal crystallization and cycle time. Plastics are also very poor thermal conductors. If it is possible to choose an amorphous plastic it will usually offer the most attractive process calculus.
There are many other thermoplastic, thermosetting and rubber processes that cannot be covered here.
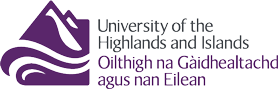
All efforts have been made to ensure materials created by the EDU comply with current accessibility guidelines (JISC: Support for learners with disabilities).
If further assistance is required with accessibility matters please contact the student support section in your academic partner UHI: Accessing learner support.
We welcome any comments on how to improve this unit. Please feel free to pass these on at any time.
If you have any difficulty viewing this resource please contact EDU (edu@uhi.ac.uk) with:
- the name of the resource;
- a description of the problem (please give as much detail as possible);
- the section of the resource where the problem occurred;
- your internet browser (you can check your browser version at: http://detectmybrowser.com/).
UHI provides links to external sources of information and may refer to specific Web sites, products, processes or services within this resource. Such references are examples and are not endorsements and whilst every effort is taken to ensure the accuracy of information provided UHI is not responsible for any of the content or guidance. You are advised to exercise caution.
Audio
Video
Reading
Download
Information
External link
Activity
Question
Asterisk
Discussion
Collaboration
Reflection/journal/log
History
Pause for thought
Download a copy of this resource in PDF format.
You can also print individual pages by printing directly from the browser.